A galvanização é um processo de revestimento de metais com uma camada de zinco para protegê-los da corrosão. Esse processo é frequentemente usado em objetos de metal, como tubos, chapas, parafusos, pregos e outros componentes de construção.
Existem duas técnicas principais de galvanização: galvanização à fogo e galvanização eletrolítica. Na galvanização a quente, o metal é mergulhado em um banho de zinco fundido a uma temperatura elevada, fazendo com que o zinco se funda e adira ao metal. Na galvanização eletrolítica, o zinco é depositado na superfície do metal por meio de eletrólise.
A camada de zinco na superfície do metal protege-o da corrosão, pois o zinco é mais reativo do que a maioria dos metais comuns. Quando exposto ao ar e à umidade, o zinco forma uma camada de óxido que impede que a umidade e o ar cheguem ao metal subjacente, protegendo-o da corrosão
Leia também: O que é desgaste por corrosão?
A galvanização tem sido historicamente utilizada para redução da corrosão atmosférica em tubulações e estruturas metálicas. Ela resulta numa proteção catódica, utilizando o zinco como ânodo de sacrifício em superfícies metálicas. No entanto, a dificuldade de aplicação da galvanização em superfícies complexas acaba resultando em diversos problemas de retrabalho.
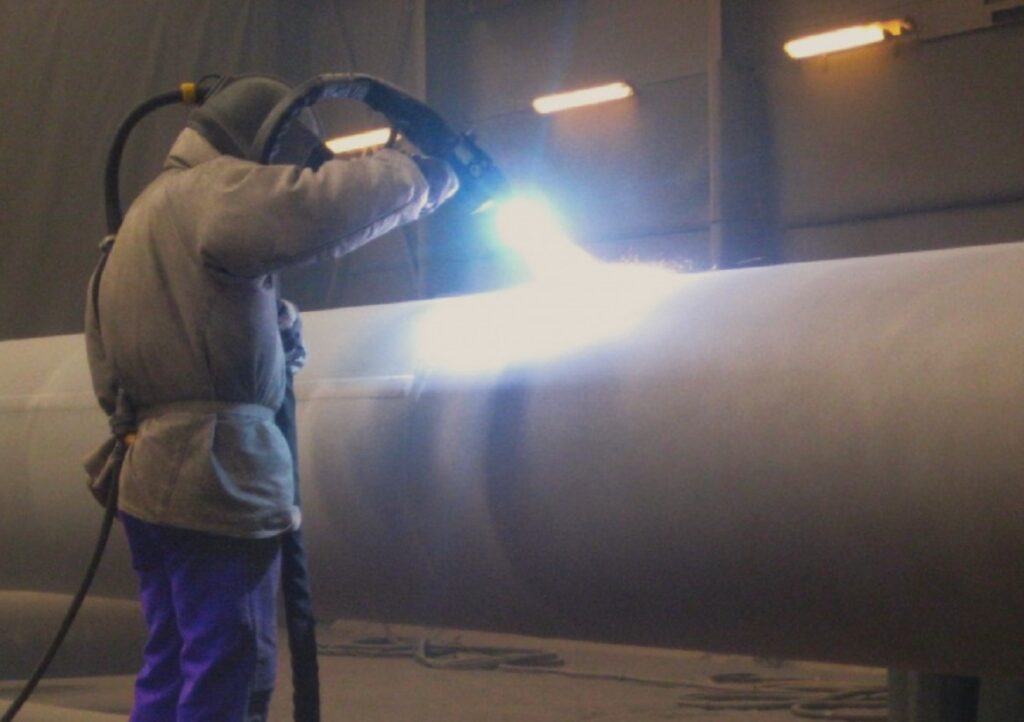
O revestimento de zinco aspergido (aplicado por aspersão térmica), tem se mostrado uma alternativa bastante viável para a substituição da galvanização em inúmeras situações. Além de ser um processo mais versátil, ele garante resultados superiores para proteção galvânica de superfícies, quando comparados com o processo de galvanização. Além dos resultados técnicos, a versatilidade do processo permite aplicações in loco.
Quais as principais vantagens da deposição do zinco aspergido em relação aos processos tradicionais?
A aplicação de revestimento de zinco por aspersão térmica, também conhecida como metalização, é um processo de revestimento no qual o zinco é pulverizado na superfície do metal com uma pistola de ar comprimido. Esse processo difere da galvanização à fogo, que envolve a imersão do metal em um banho de zinco fundido ou da galvanização eletrolítica, que também requer a imersão das peças em um banho.
Algumas vantagens da aplicação de zinco por aspersão térmica em relação aos tradicionais processos de galvanização
- Menor deformação do material: A aspersão de zinco envolve temperaturas mais baixas do que a galvanização a à fogo, o que significa que o metal é menos propenso a deformações resultantes do processo de aplicação.
- Maior versatilidade: A aspersão térmica de zinco pode ser usada em uma variedade de metais, incluindo aço, alumínio e metais não ferrosos, enquanto a galvanização a quente é mais adequada para aços carbono e de baixa liga. Além disso, o processo de aspersão térmica permite a aplicação do revestimento no campo. Dependendo do tamanho da peça não compensa fazer a movimentação até o prestador de serviço.
- Maior resistência à corrosão: A galvanização por aspersão térmica pode produzir um revestimento mais resistente à corrosão por que permite uma espessura maior do revestimento depositado. Além disso, pode ser utilizado um selante polimérico, que aumenta ainda mais essa essa resistência. O revestimento de zinco também atua como proteção catódica
Quais as principais desvantagens desse processo em relação aos processos de galvanização?
Assim como em qualquer outro processo, a aspersão térmica de zinco não é substituta pra 100% dos casos de aplicação de zinco por galvanização. Pode parecer contraditório, mas uma das vantagens do zinco aspergido é também uma desvantagem. Vaja abaixo as principais desvantagens desse processo:
- Espessura da camada. A espessura da camada do zinco aplicado por aspersão térmica normalmente é superior à 0.1 mm, o que inviabiliza, por exemplo, a aplicação desse tipo de revestimento em roscas devido ao fato de não ser possível manter o seu perfil.
- Nível de desperdício. Em peças com pouca área de aplicação (como em telas, por exemplo, o nível de desperdício de material é muito elevado, o que torna o processo mais oneroso.
- Produtividade com peças à granel: em muitos casos, peças à granel, de dimensões pequenas, teriam que ser feitas uma a uma, o que torna o processo lento, com alto nível de desperdício, e consequentemente mais oneroso.
O zinco aplicado por aspersão térmica é então voltado para peças de maior porte e com maiores áreas de aplicação.
Case de sucesso do uso Zinco Aspergido para substituir a Galvanização
Foram realizados testes de corrosão em câmara de névoa salina, de acordo com a norma ASTM B 117 com diferentes camadas em ambos os processos.
Num primeiro momento as amostras permaneceram no interior da câmara por 120 horas. Nesse período, todas as amostras que passaram pelo processo de galvanização apresentaram corrosão vermelha, enquanto as amostras revestidas com zinco aspergido não apresentaram nenhum sinal de corrosão. Essas amostras foram deixadas no interior da câmara por mais 92 horas e mesmo assim não demonstraram sinais de corrosão.
Alguns exemplos de aplicação do revestimento de zinco aspergido: Torres de geradores eólicos, estruturas metálicas em plataformas de petróleo, carcaças de bombas, carcaças de válvulas de esfera, etc.
Baixe a seguir aqui o E-book: “Revestimentos Metálicos Contra Corrosão”.